Grievance Mechanisms
When workers have a safe and accessible way to report issues in their workplace, conditions improve.
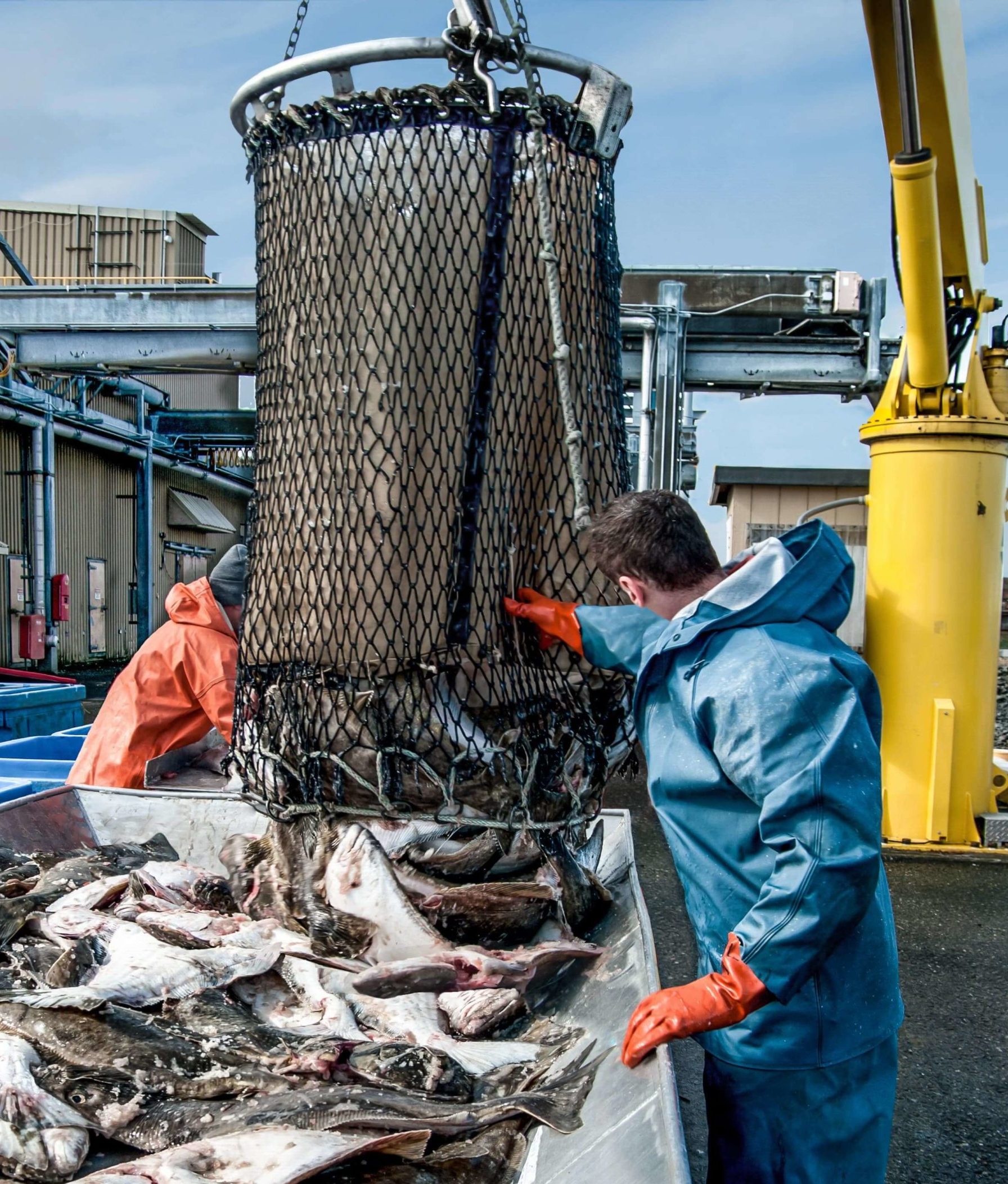
In seafood supply chains, workers are often migrants, some doing dangerous work in situations with limited oversight. Many are at sea, separated from their community for extended periods. They need accessible grievance mechanisms that respect privacy and dignity and lead to effective remediation. When implemented well, these mechanisms ensure transparency, accountability, and continuous improvement of working conditions across supply chains.
What is a Grievance Mechanism?
Grievance mechanisms are formal complaint processes that can be used by stakeholders, including workers and community members, to raise concerns if they are being negatively affected by business operations. Grievance mechanisms are a key tool to address human rights violations and to promote decent work in seafood supply chains. They provide workers with a safe and accessible way to report issues, seek remedy, and improve workplace conditions. When designed and implemented effectively, grievance mechanisms not only support early identification of risks but also help you build trust with workers, address issues before they escalate, and strengthen your human rights due diligence efforts.
Grievance mechanisms provide significant benefits in the workplace. They facilitate communication between workers and management around workplace problems and enable workers to submit complaints with dignity, knowing that there is a system to fairly evaluate their complaints.
Effective Grievance Mechanisms
The United Nations Guiding Principles for Business and Human Rights has identified eight criteria for evaluating the effectiveness of grievance mechanisms:
- Legitimate, enabling trust with workers and establishing accountability for the fair conduct of the process.
- Accessible, known to all workers and providing adequate assistance to workers who face barriers to access.
- Predictable, providing clear and known procedures with a time frame for each stage and clarity on the process, ownership, and outcome.
- Equitable, giving workers access to sources of information, advice, and expertise to help navigate the process.
- Transparent, keeping those involved in the process informed about progress and providing sufficient information to build confidence in its effectiveness.
- Rights-compatible, ensuring outcomes and remedies are in line with internationally recognized human rights.
- A source of continuous learning, using review and evaluation to identify ways to improve the grievance mechanism and prevent future grievances and harms.
- Based on engagement and dialogue, consulting with workers on policy and process design and focusing on dialogue as the means to address and resolve grievances.
The first step to developing effective grievance mechanisms is to outline the structure and process for receiving, reviewing, and remediating grievances. Procedures should be designed so that they provide for a real and concrete settlement, not simply give a series of administrative steps that need to be taken before the issue can be concluded. Grievance mechanisms should include:
- Policies to allow workers to report grievances without fear of penalty, dismissal, or reprisal.
- A way to ensure worker confidentiality.
- Procedures to allow workers to report issues to someone other than their supervisor or a manager in their supervisor’s chain of command.
- Procedures for workers to monitor the status of complaints.
- A procedure for management to follow up on reported grievances.
- Policies to give workers access to additional support or advocacy.
- Policies to allow workers to be supported or represented by a trade union or party of their choosing.
- A way to appeal.
In order for grievance mechanisms to function properly, everyone involved in the process must be properly informed and trained. Train workers on how to use the grievance reporting tool and what will happen after an issue is reported. Train supervisors, managers, and owners on the grievance mechanism, with attention to confidentiality and non-retaliation.
Grievance mechanisms in seafood supply chains should include consideration for accessibility, language barriers, and stakeholder involvement. To ensure freedom of communication and the ability to access grievance mechanisms for workers on board vessels, require and implement Wi-Fi access on ships, with an access agreement that includes terms, hours of use, and privacy stipulations. Workers should have the same level of access to Wi-Fi as the captain. Since seafood supply chains and workplaces include workers speaking different languages, ensure that grievance mechanism policies, procedures, and tools are available in all of the primary languages spoken by workers. Because of the number of migrant workers and their distance from direct support, work with trusted local organizations. Form partnerships with external technical experts as needed and leverage local support to communicate with worker families, unions, and other stakeholders who can support grievance resolution.
Addressing Worker Grievances
Address issues in a timely manner when responding to grievances submitted by workers. Include a time-bound process that ensures credible remedy, followed by verification from workers that remediation has occurred. Address grievances in four steps:
- Analyze and verify the problem, involving those impacted in the process.
- Include those impacted and all levels of management when designing a solution that addresses the problem’s root cause and prevents further issues.
- Consult with workers and integrate worker-led efforts into the remediation process.
- Work with suppliers to respond to grievances or human rights abuses with a time-bound corrective action plan.
- Work through your supply chain partners in order to prevent confusion and avoid undermining other efforts.
- Resolve the operational issues contributing to the problem and reduce the likelihood of similar issues occurring in the future, by addressing the root cause.
- Consider potential roadblocks and engage with those that can help you move past them.
Throughout the remediation process, communication is essential. Include guidance on when communication will be provided after the grievance is submitted. Workers and management should be updated regularly before resolution is reached. Provide workers access to a case management system with support and protection in order to ensure follow-up and communication, and safeguard them from threats or retaliation.
These resources can help you design mechanisms that are more accessible, trusted, and aligned with international standards, ultimately creating safer and more responsive supply chain environments:
- To support continuous improvement and strengthen grievance mechanisms across seafood supply chains, see the ILO’s guidance on grievance handling for an overview of effective workplace procedures.
- To integrate grievance processes into broader human rights due diligence, see the “Early Warning, Effective Solutions” guide by the Global Compact Network Netherlands, Oxfam, and Shift, which outlines practical steps for remediation and stakeholder engagement.
- To find seafood-specific guidance, see Human Rights Due Diligence: Fundamentals for Impactful Implementation in Seafood, which highlights industry-relevant considerations and best practices.
- For tips on evaluating and improving grievance systems, see Step 6 of Verité’s Fair Hiring Toolkit, “Establishing Effective Grievance Mechanisms & Protection for Whistleblowers” and related tools for assessing performance.